Description
Polycarboxylate Concrete Accelerator
In the mid 1990s, polycarboxylates(i) in HRWR admixtures were presented in North America, accordingly starting an emotional worldview change in our comprehension of how to outline and utilize very workable solid blends. Due to the adaptability, improved workability, workability maintenance with negligible set hindrance, and great completing attributes, the acknowledgment bend for these admixtures was much shorter than anything beforehand presented.
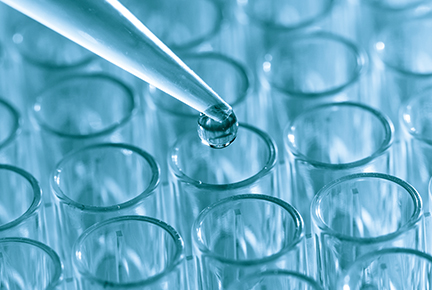
Polycarboxylate Concrete Accelerator, Cement Tiles Hardener, chemical admixtures for concrete, Concrete Accelerator, Concrete Chemicals, Concrete Tiles Chemicals, Concrete Tiles Hardener, Interlocking Tiles Hardener, Polycarboxylate admixtures, polycarboxylate ether-based superplasticizers, Superplasticizers.
1 | Discription | Clear liquied | Complies |
---|---|---|---|
2 | % BASE Assay | 40 % Min | PASSES |
3 | Insoluble matter | NIL | PASSES |
4 | PH OF 5% | Aqueous6.0 TO 8.0 | PASSES |
5 | Solution | NEUTRAL | |
6 | specific density | 1.4 |
Not long after the presentation of polycarboxylate-based HRWRs or Polycarboxylate Concrete Accelerator, solid makers started trying different things with SCC in all fragments of solid creation; be that as it may, no place was SCC more quickly acknowledged than in the precast business sector. The capacity to fill a mold rapidly without vibration, while as yet keeping up or notwithstanding enhancing the plastic and solidified properties of the solid, made SCC a flawless match for precast solid makers.
Precasters started utilizing terms like droop stream, thickness, filling capacity, passing capacity and rheology to portray this progressive kind of self-merging and non-isolating cement. Not at all like prior HRWR innovations, for example, naphthalene (C10H8) and melamine sulfonate (CH3SO2O) condensates, which have altered science and constrained execution ability, polycarboxylate innovation is exceptionally adaptable, implying that the polycarboxylate polymer can be planned and improved for an extensive variety of execution necessities, from high early quality to stretched out droop life to SCC.
With the rise of SCC, another class of substance admixtures – consistency adjusting admixtures (VMAs) – has been marketed to address the requirement for enhancing the water resilience and isolation resistance of this exceedingly flowable cement. The fast acknowledgment of VMAs provoked the consideration of another admixture class, Sort S, in the ASTM C494 standard to guarantee clients that VMAs have no effect on normal solid properties (workability, set, quality and shrinkage).
Where are we now ?
A rundown of the latest concoction admixtures applicable to precast cement is as per the following:
Universally useful polycarboxylate-based HRWRs – A HRWR for high stream (≤10 in.) and/or low w/c proportion cements (≥ 0.40). These superplasticizers would not as a matter of course be connected for a unique execution, for example, high early quality or self union.
High Early Quality – A polycarboxylate-based HRWR composed and planned to empower expanded quality at ahead of schedule ages.
Developed Droop Life HRWR – These admixtures are normally mixes of diverse polycarboxylates, which are built to initiate or increment droop at distinctive times. The objective of these polycarboxylate-mixed items is to keep up solid blends at target workability levels until cement is set and solidified without postponing set times. A few HRWR items have been as of late presented, included exclusively of gradually actuating polycarboxylates, which can be added to any solid blend to amplify droop life as craved.
Rheology Changing Admixtures – These admixtures are intended to confer lubricity to the solid, particularly at low droops, bringing about enhanced shaped completion, expanded profitability and enhanced surface composition.
Thickness Changing Admixtures (VMAs) – Consistency altering admixtures are most ordinarily utilized as a part of SCC when the group to-bunch varieties in total degree, molecule shape and thickness, and water content make it hard to reliably create a stable, non-isolating SCC blend. VMAs capacity by building a system structure inside of the pore water that minimizes water and glue development, particularly once the solid is in a static state. VMAs have likewise been utilized with ordinary cement blends where the solid blend might tend to isolate.
Shrinkage Decreasing Admixtures (SRAs) – SRAs give some measure of lessening the potential for autogenous shrinkage breaking with superior solid (w/c proportion < 0.40).
What Would be an ideal Next Step?
Polycarboxylate HRWRs will keep on being the predominant admixture innovation, particularly in precast cement. As an aftereffect of persistently enhancing the measurement proficiency of polycarboxylates, they are now infiltrating into ordinary water-lessening and water-diminishing/impeding concoction admixtures. Building or outlining polycarboxylates to make or alter a particular execution quality of the solid blend will likewise
Cracks in Concrete Paving Blocks a common problem in precast concrete industry.
WHY CONCRETE CRACKS :-
One of the most common questions received on our Email is about cracks that are developing in newly poured concrete. The homeowner will question why it is cracking and did they receive a shoddy job.
When installed properly, concrete is one of the most durable and long lasting products you can use around your home. But it is important that concrete contractors follow well-established guidelines with respect to concrete placement. Durable, high strength, and crack resistant concrete does not happen by accident.
Why Concrete Cracks
Reason #1 – Excess water in the mix
Concrete does not require much water to achieve maximum strength. But a wide majority of concrete used in residential work has too much water added to the concrete on the job site. This water is added to make the concrete easier to install. This excess water also greatly reduces the strength of the concrete.
Shrinkage is a main cause of cracking. As concrete hardens and dries it shrinks. This is due to the evaporation of excess mixing water. The wetter or soupier the concrete mix, the greater the shrinkage will be. Concrete slabs can shrink as much as 1/2 inch per 100 feet. This shrinkage causes forces in the concrete which literally pull the slab apart. Cracks are the end result of these forces.
The bottom line is a low water to cement ratio is the number one issue effecting concrete quality- and excess water reduces this ratio.
What you can do about it:
Know the allowable water for the mix the contractor is pouring- or be very sure you have chosen a reputable contractor who will make sure the proper mix is poured. It is more expensive to do it right- it simply takes more manpower to pour stiffer mixes.
Reason #2 – Rapid Drying of the concrete
Also, rapid drying of the slab will significantly increase the possibility of cracking. The chemical reaction, which causes concrete to go from the liquid or plastic state to a solid state, requires water. This chemical reaction, or hydration, continues to occur for days and weeks after you pour the concrete.
You can make sure that the necessary water is available for this reaction by adequately curing the slab.
What you can do about it:
Read here about the methods to cure concrete and understand how your contractor will cure the concrete.
Reason #3- Improper strength concrete poured on the job
Concrete is available in many different strengths. Verify what strength the concrete you are pouring should be poured at.
Talk to the ready mix supplier
Consult with the Ready Mix Concrete Association in your area.
Reason #4 – Lack of control joints.
Control joints help concrete crack where you want it to. The joints should be of the depth of the slab and no more than 2-3 times (in feet) of the thickness of the concrete (in inches). So 4″concrete should have joints 8-12′ apart.
Read more about control joints here.
Other reasons:
Never pour concrete on frozen ground.
The ground upon which the concrete will be placed must be compacted.
The sub grade must be prepared according to your soil conditions. Some flatwork can be poured right on native grade. In other areas 6″of base fill is required along with steel rebar installed in the slab.
Understand what you contractor is doing about each of the above listed items and you will get a good concrete job.
*Our Cement Hardener Chemical come with 100% Money Back Guarantee . Please try samples before Mass use. We Provide 100% Money Back Guarantee maximum value upto 100kg of our Chemical. Please try Small Cement Hardener Chemical packing samples Before use in mass production. Please follow proper user guide to avoids mistakes. in case of return freight for both side pay by buyer. SRI KRISHNA PLASTO shall have no liability whatsoever for loss or damage to the Goods transportation damage.